The Essential and Exciting Safety Technologies for Manufacturers
- Ram Soundararajan
- Oct 29, 2021
- 4 min read
Updated: Mar 18, 2024
Health and Safety functions in companies have historically focused on robust processes, audits, inspections, training, metrics, PPE and permits to keep people safe in the workplace. These no doubt are cornerstones of any good EHS program. But EHS functions across the board have been guilty of not adopting technology sufficiently and fast enough to improve health and safety outcomes and processes in the workplace.
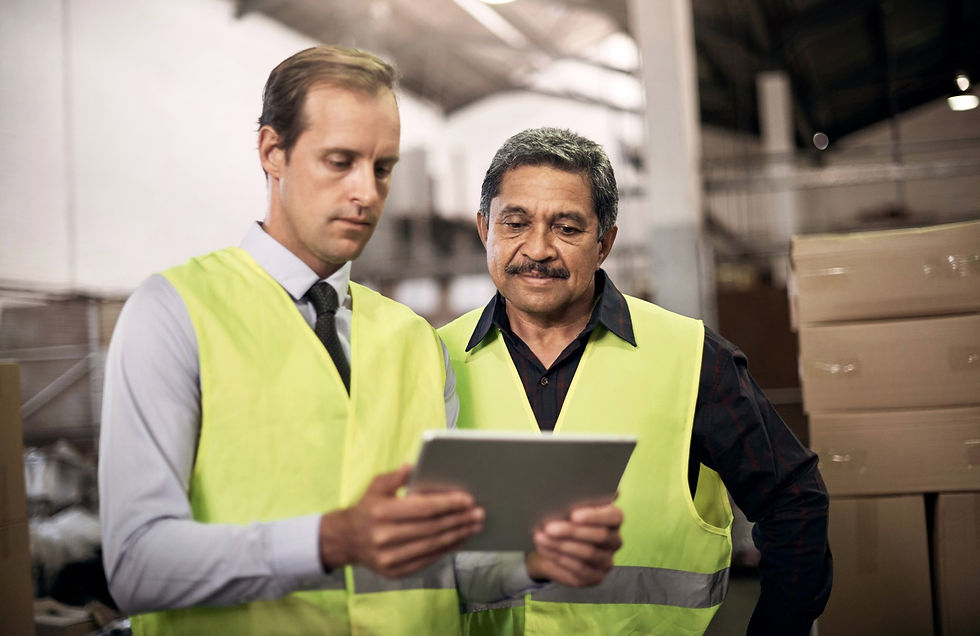
We discussed technology adoption with several EHS leaders across the world and have presented technologies that will define the future of EHS outcomes. We have categorised these as Must Have, Good to Have and Nice to Have technologies.
Must Have Technologies:
Simple, Affordable EHS Management Software
Over 85% of companies still manage their EHS processes manually through pen, paper, and spreadsheets. Majority of companies that have some EHS management systems still only focus on incident recording and reporting. The advent of cloud computing and SaaS business models allow companies to do away with archaic and disjointed systems to a unified, simple, affordable EHS software. SafetyQube is one such affordable software and there are a handful of good EHS software products out there. These enable you to stay on top of hazards, incidents, audits, inspections, risk assessments, analytics, reporting documentation etc and save EHS teams loads of time and effort. These are also handy when safety certification audits are around the corner. Furthermore, proactive Health and Safety regulators may mandate companies in the future to use such software for EHS record keeping and reporting.
Mobile Enabled EHS Management Software
Mobile phones and tablets have become increasingly prevalent on shop floors and work areas. Mobile apps and phones make it easier for frontline workers to actively participate in health and safety improvement. These take away the implementation effort associated with desktop only systems. Mobiles / tablets widen access to broader workforce and are more intuitive to use. After all who ‘IMPLEMENTS’ an app? Companies can download these apps and use the system immediately after just a few simple configurations. Mobile access and resulting participation widen the hazard funnel and make inspections and risk assessments easier. Often affordable EHS software systems have excellent ROI through reduced lost time, litigation, and business insurance costs.
Lone Worker Safety Software
Companies with individual field workers could benefit from adopting such software. Such software tracks their location, allows them to share their safety status, receives alerts and communication in the event of non-response, raise alarm in case of danger, allows them to inform the company before they perform a task in a hazardous area (e.g. confined spaces). Such software is typically a mobile app. It is important to note any software that tracks people’s location and details etc. suffer from data privacy concerns of both users and companies.
Good to Have Technologies :
Wearables
Wearables allow companies to track measurable employee health and activity parameters and allow employees to communicate swiftly in case of unsafe situations. Wearables can be creatively used to push alerts, notifications and monitor specific safety requirements and conditions. These too however suffer from data privacy concerns.
Automated Warning Systems
Early warning systems use sensors, cameras, RF tags etc to alert a worker about a potential unsafe condition. For example, imagine a vibrating element fixed under the seat of a vehicle driver. A camera inside the vehicle monitors the eye movement of the driver and when it detects the driver may be falling asleep while driving, the vibrating element is activated to alert the driver. Or say a technician must work in a high temperature or high noise area, the sensors alert the technician if temperature or noise levels raise above certain levels. Forklifts can automatically slow down when they are within a certain distance from a human or an object. These technologies are fragmented and are typically very selectively adopted.
Nice to Have Technologies :
Virtual Reality
VR based safety training is slowly catching up as operators, technicians and engineers can all train in a less risky environment. VR technologies allow multiple people to be trained at the same time and without stopping equipment, like how airplane pilots train with a simulator. Imagine a fire evacuation drill or a lockdown procedure is conducted in VR. Research shows people learn better from these than from videos, though these are expensive methods for small and medium companies.
Connected PPE
Connected PPE offerings like connected safety shoes, helmets, safety harnesses, goggles, gas masks have increasingly been introduced over the last 3+ years into the market. These can also automatically detect what PPE is needed where / when and relay information over the internet about PPE conformance or non-Conformance when an activity is performed in a hazardous environment. It is still very early days for these technologies and are selectively adopted, mostly by large companies.
AI Enabled Visual Inspection Technologies
Visual inspection technologies can connect to cameras positioned in critical locations to visually monitor employee and equipment activities. They then use artificial intelligence to identify safe / unsafe acts (e.g. PPE conformance) hazards, near misses and incidents and automatically send alerts. This technology is still in its early stage and has concerns around accuracy and privacy. There are also issues around getting trade union / work council support for such technologies to be deployed.
Health and Safety functions in many organisations still rely on 20th century technologies. With the current labour and skill shortages in manufacturing, warehousing, logistics and construction, companies need to graduate to 21st century technologies that demonstrate progressive approach to people safety, to attract and retain talent. At the minimum, companies need to adopt affordable ‘Must Have’ products like SafetyQube to ensure they are not left behind.
Comments